Seztec’s Minisonic Ultrasonic Clamp-On Flow Meters are the perfect solution for measuring multiple key parameters in heating or cooling HVAC systems! Whether you need to track supply and return water flow, CHW pump flow, or check metering, these flow meters provide accurate results every time. In addition, they are ideal for hydraulic balancing, leak detection, supply and return temperature measurements, and even heating or cooling energy consumption (BTU). So if you want to improve the efficiency and performance of your HVAC system, choose the Minisonic Ultrasonic Clamp-On Flow Meters by Seztec!
Applications of Ultrasonic Clamp-On Flow Meters in HVAC Industry
Experience the versatility and convenience of Minisonic flow meters with both Portable and Fixed options! The Minisonic II Portable offers mobility and on-site measurement capabilities, while the Minisonic Fixed offers a permanent solution for your flow measurement needs. Choose the right option for you and enjoy accurate and reliable flow measurements with Minisonic.
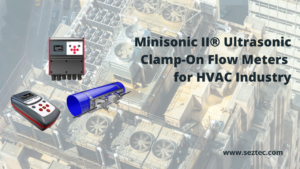
Minisonic II Fixed Ultrasonic Flow Meter:
The Minisonic II fixed flow meters are a highly efficient solution for measuring heating or cooling energy consumption (BTU) in HVAC systems. These meters are ideal for cost allocation and sub-metering applications. Their versatile design enables them to be deployed in a wide range of applications in HVAC systems, including chiller supply headers, condenser lines, main chilled water headers, supply and return lines for chilled and hot water, boilers, and heat exchangers, with a large diameter range capability up to DN 10,000.
Minisonic II Portable Ultrasonic Flow Meter:
Unlock the full potential of your HVAC system with the Minisonic II Portable Ultrasonic Flow Meters! Whether it’s optimizing pump flow, conducting hydraulic balancing, performing flow surveys, verifying flow meters, or detecting leaks in your CHW or hot water network pipes, these portable flow meters are the ideal solution for all your maintenance needs. Get ready to take your HVAC system to the next level!
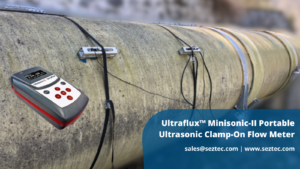
Measuring Principle:
The Minisonic Ultrasonic Flow Meters utilize the transit-time technology, which is based on the principle of time-of-flight, to determine the velocity of fluid flow and the volumetric flow rate. The device comprises two transducers that alternate in emitting and receiving ultrasonic signals. The difference in transit time between the transmitted and received signals is directly proportional to the liquid flow rate and is used to calculate it.
HVAC Challenges:
The HVAC system in a building is a critical component in ensuring the comfort and safety of its occupants. However, it is prone to several mechanical and hydraulic issues that can cause energy losses and affect the efficiency of the system. The Minisonic II Flow Meter offers a solution to these common HVAC challenges:
(1) Pumping and Insufficient Water Flow Issues
One major inefficiency in a heating or cooling system is related to water flow problems within the system. Over time, pumps can experience internal wear and tear that decreases their overall efficiency and affects their ability to provide the specified water flow (gpm) to the system. Insufficient water flow through the system can cause significant damage to the chillers and can also cause the pipes to freeze. Therefore, monitoring pump flow and chiller flow accurately is critical to the well-being of your HVAC system.
(2) Hydraulic Balancing
Water-cooled chillers reject absorbed heat through an additional water loop, called condenser water lines, which feed heated water to the cooling towers for cooling. A building may have more than one cooling tower to meet its energy demand. To ensure maximum cooling efficiency, the operator must ensure an equal amount of water flows through each cooling tower/cell. The Minisonic II Flow Meter can be installed on the condenser pumps to accurately measure the condenser water flow reaching the cooling towers. This information can help the operator optimize their pump flow for maximum cooling efficiency.
(3) Energy Loss at Low Water Flow Rates
During low-demand times, the building may consume much lower cooling or heating energy. Accurately measuring these low flow rates is crucial as energy transfer at low water flow rates typically goes unmetered, effectively giving away “free energy.” The Minisonic II Flow Meter can measure extremely low flow velocities (0.03 ft/s), ensuring that no energy goes unmetered and providing maximum return on investment to energy producers.
(4) Maintenance Costs
Maintenance costs are a significant operating cost of a heating or cooling system, including pump overhaul, chiller overhaul, insulation costs, flow meter or BTU meter recalibration and replacements, water leaks, water treatment, etc. The Minisonic II Flow Meter is a 100% clamp-on solution and does not require any pipe cutting for installation, removal, or replacement. The flow meter can be retrofitted at any location within your HVAC system and can be moved to a different location in the future without requiring a system shutdown. As the flow sensors are attached externally to the pipe, they do not come into contact with the liquid, ensuring the flow meter will not require maintenance or recalibration throughout its lifespan. Furthermore, the Minisonic II flow meter features permanent ultrasound coupling pads (elastomer pads), replacing the traditional ultrasound gel that can wash away due to pipe condensation on CHW pipes. The permanent coupling pads eliminate the need for periodic flow meter maintenance to reapply ultrasound gel, keeping your maintenance and operating costs low.
(5) Network Water Leaks
Chilled water systems, especially in district energy plants, are connected to a vast network of underground insulated water pipes that stretch for miles. These lines are typically unmetered, and any network leaks go undetected. By retrofitting with the Minisonic II non-intrusive flow meter, operators can monitor supply and return water flows in the main headers and individual branches to detect water leaks, without the need to meter the entire network.
In conclusion, the Minisonic II flow meters are a reliable and efficient solution to meet the challenges faced by HVAC systems. These flow meters provide accurate and non-invasive measurement of liquid flow rate, ensuring maximum efficiency and cost savings. With its large pipe diameter range, the Minisonic II can be installed in various points in the HVAC system, making it a versatile and adaptable solution. Additionally, its maintenance-free and retrofit nature, reduces the overall maintenance costs and downtime of the HVAC system. In short, the Minisonic II flow meters are the ideal choice for building owners, plant operators, and engineers who strive for maximum energy efficiency, cost savings, and hassle-free operation of their HVAC systems.
We offer flow meter rental service so you can carry out pump flow verification, flow meter verification, and hydraulic balancing at your cooling plant. Our rental solutions are 100% non-intrusive, meaning no pipe cutting needed to make measurements.
Here is an interesting case study about hydraulic balancing where we helped a cooling plant optimize their condenser water flow.
Contact us today with your measurement problem!
www.seztec.com | sales@seztec.com
Published by:
Seztec USA
copyright © 2022 Seztec LLC
Published on: May 12, 2022 at 19:01